“Clay acts almost as an antidote to the overwhelm of the digital world.”
-Jennifer Waverek.
According to the writer of “Pottery-making Cultures and Indian Civilization,” Khurja is among the oldest cities for India’s pottery. It is a small town in the Bulandshahr district of Uttar Pradesh, India. It is approximately 90 kilometers from Delhi. Khurja is also known as “The Ceramic Town” because it supplies a large portion of ceramics and pottery used in India. This creative pottery is the source of earning for a large number of artisans of Khurja.
History of Khurja
At least two different stories have come up about the origins of Khurja’s pottery work. As per one of the chronicles, over 500 years ago, people with knowledge of pottery from Egypt and Syria accompanied the Afghan King Taimur Lung when he passed by Khurja during an easterly campaign over 500 years ago. They actually started with red clay pottery and progressed to blue glaze. They painted floral designs with cupric oxide on the red clay articles with a white covering and applied a soft glaze containing glass and borax, among other things, to them.
Another anecdote claims that potters were relocated to the area during the Mughal Empire, while another claims that there were no long historical events associated with pottery tradition in Khurja. As mentioned in one of the books “These potters often call themselves as Multani Kumhars suggesting that their origin was Multan”.
Making Of Khurja
The making of Khurja involves the following process:
Preparing the Clay
Clay is the primary raw material used in ceramic pottery and is obtained from various locations throughout the country, including Kerala, Rajasthan, Delhi, Bikaner, Bihar, and Ahmedabad.
Clay mixed with various materials such as quartz, potash feldspar, china clay, and ball clay procured from Jaipur, Ahmedabad, and Bikaner, Kundan clay from Kerala, Rajmahal clay from Bihar, and fire clay from Delhi is the main raw material used in ceramic pottery.
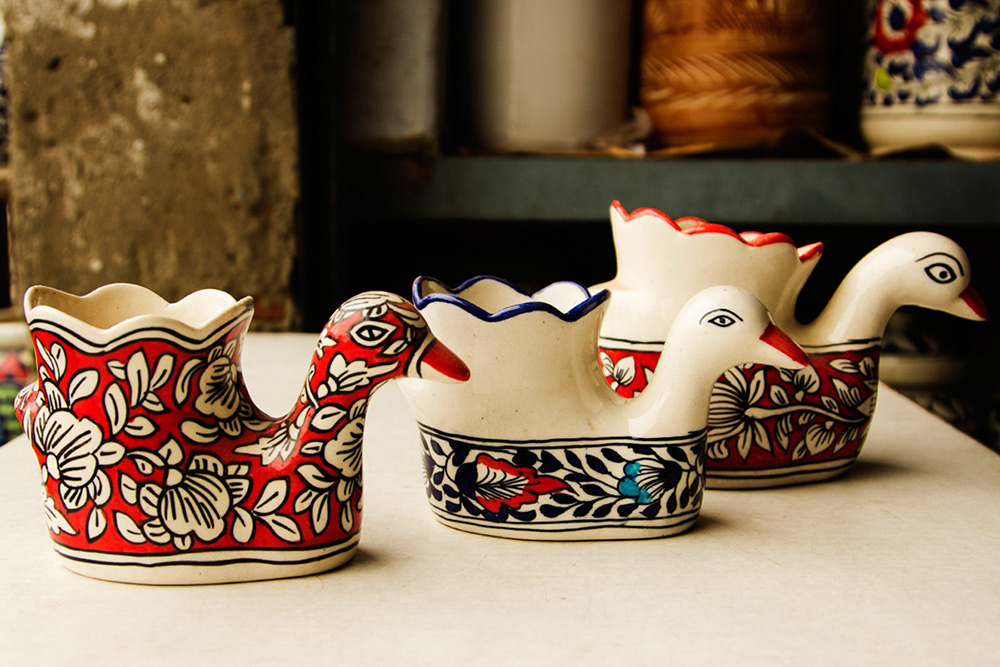
All these raw materials are mixed in a secret ratio (trade secret) and ground in Ball-mill equipment for around 10 hours to get a homogenous mix of clay dough. It is further pressed between the metal plate and canvas cloth to remove the excess water content and a clay disc of size around 1.5 feet diameter is produced.
Clay Moulding Process
Plaster of Paris is used to create a mold of the needed piece with the product cavity (POP). As a material, clay is combined in a liquid solution with no lumps and poured into the mold until the solution fills the hole. When the article’s wall reaches the required thickness, the mold box is gently shaken to remove air bubbles and surplus clay liquid solution is dispensed. After settling time, the molded product is scraped using a blade from the rim and other surfaces of the mold. For a day, the products are dried at room temperature.
Jigger and Jolly Process:
In this process, the products are made with equipment called Jigger and jolly, which contains a die in jigger and a cavity in jolly to shape the clay.
Smoothening Process
Semi-finishing is used to improve the surface finish of dried products by sanding uneven surfaces and parting lines with sandpaper. Any Cracks that appeared during the molding process are additionally filled with clay and sanded after drying. Sanded items are properly cleaned with a cotton cloth and cold water.
Painting Process:
Mughal art and regular painting with motifs on the exterior surface are the two types of painting on ceramic pots. Mughal art is painted with a cobalt-blue color and a colorless lead glaze, whilst sketching designs like as floral or geometric patterns on the outside surface using oxide colors and a colorless lead glaze is another genre. Ceramic objects gain value by being painted on a plain surface.
Sticker Ornamentation:
Sticker ornamentation is another method of adding value to ceramic products like coffee mugs and crockeries, mainly used for advertising, better aesthetics, and to display corporate identity.
Glazing process:
Glazing is a glossy covering fused to ceramic artifacts that colors, decorates, waterproofs, and strengthens the underlying ceramic.
Firing Process:
Previously, a brick kiln was used, but currently, a gas or electric kiln with temperature control technology is used. It makes it easier for artisans to work and reduces the amount of damage. The articles are baked for approximately 20 minutes at 1200 degrees. A glossy surface is obtained by firing at 1200 degrees for over a minute. A matte or non-glare finish is obtained by firing at temperatures between 1100 and 1150 degrees. Finished pieces are dispatched for packaging.
Evolution of Khurja pottery
Various metals used to make household utensils were banned during WWII, and imports of ceramic goods were severely restricted. The Government of Uttar Pradesh established a ceramic unit in 1942 to meet the demand for ceramic wares, primarily for war hospitals.
The factory was later closed in 1946–47 due to a lack of quality. The factory was renamed Pottery Development Centre in 1952. From 1942 to the present, various actors took some adoption, transformation, and initiative for the betterment of pottery manufacture. This benefitted the art immensely and opened various doors for its exposure at the national level as well as export to foreign countries.
Some facts about Khurja Ceramics
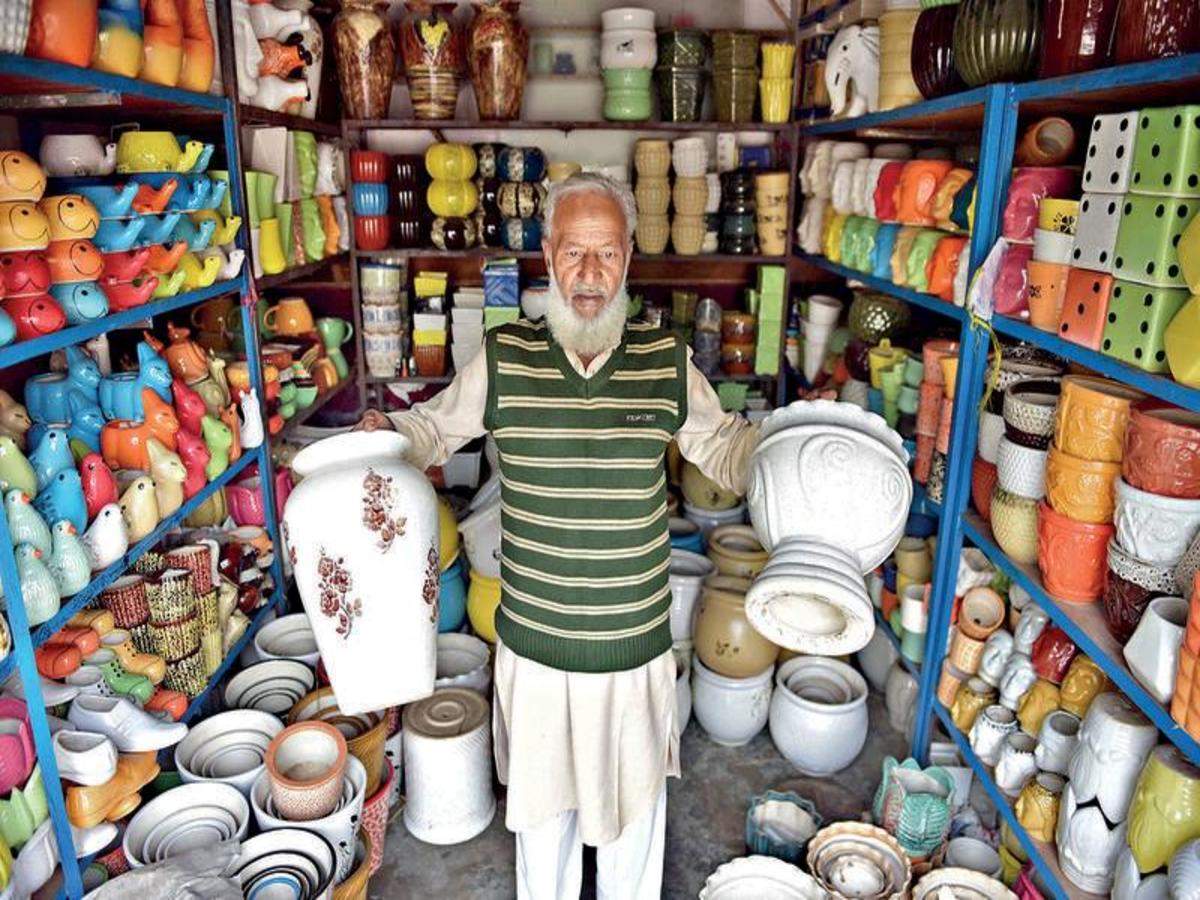
Khurja pottery has been protected under the Geographical Indication(GI) of the TRIPS agreement.
It is listed at item 178 as “Khurja Pottery” of the GI Act 1999 of the Government of India with registration confirmed by the Controller General of Patents Designs and Trademarks.
- Khurja is so popular that the place of its production is also called as ‘the ceramic town’.
- Khurja is a handicraft product that is handmade and hand painted.
- Khurja pots have a number of advantages. Its clay pots are wonderful for cooking food because they keep the PH balance, making the food less acidic and allowing it to be cooked with less oil while yet retaining all of the nutrients.
Present-day state

Presently, there are 15,000 official employees and approximately 25,000 unofficial employees who work in 500 units and nearly 400 factories. They manufacture a wide range of products, including crockery, art wares, electrical goods, sanitary wares, tiles, household items, and so on.
Khurja pottery is not only popular in India but is exported to other countries as well. There are approximately 23 export-oriented units. According to reports, the production received approximately 2,500 million Indian rupees in 1999–2000, including 148.2 million Indian rupees in export.
Don’t forget to check out our collection of the Khurja pottery at ‘The Clios Heritage Store.’